Is MMC Modern?
“The Eiffel Tower was built with 12,000 prefabricated pieces in 1889, and prefab homes were built in the UK after the Second World War ended.
Offsite manufacturing shouldn’t be seen as an early adopter, offsite should now be considered as a standard MMC process to consider.”
Jonathan Passmore, Head of Technical Sales at Helec explains.
“The modern method of construction allows Helec to build plant rooms more sustainably whilst creating less waste.
To be commercially on point, we need to construct new build plant rooms in a timely manner, so we can confidently deliver within budget for our clients for many years to come.
Offsite manufacturing
When Helec talk about manufacturing, we design & construct offsite in a quality-controlled cost-effective environment with in-house checks & balances so we deliver consistent quality and a performing “A++” rated hydronic solution for all M&E applications.
Helec build packaged plant rooms using a “standard” EnSmart design footprint to deliver LTHW & space heating & cooling, irrespective of the footprint and the energy (heat) source required by our clients’ request, or regionally set planning legislation.
The word “standard” is often problematic as people assume we are building identical boxes, but I think of it as optimisation.
We implement small changes that make optimal use of our approved design through use of our standard material components, which in turn delivers an efficient offsite built solution ready to ship to site.
Advantages
The advantage of this is we can hold stock of common materials that don’t get wasted because we design & build to size. We use standard tried and trusted components that we source locally through our key supply chain route, rather than use bespoke items that have to be pre-ordered due to long lead times, which in turn increase cost and time to deliver.
All these can be aligned for enhanced installation efficiencies.
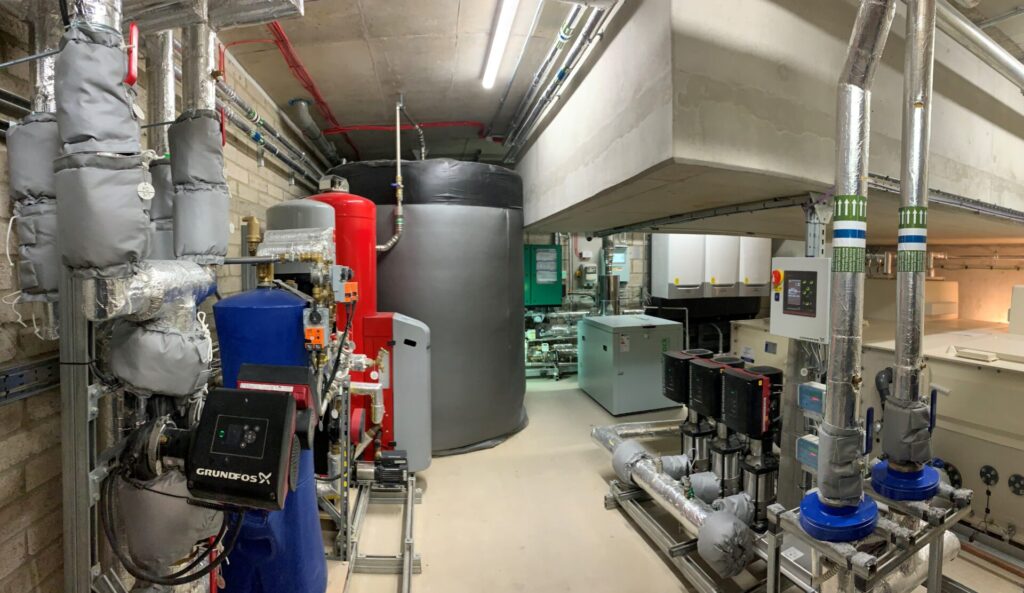
EnSmart packaged plant room by Helec
Efficient Build Strategy
By using and adapting our bill of materials, Helec has developed efficient build strategies utilising offsite EnSmart construction methods in what would normally be a long-running, highly disruptive onsite “knife & fork” build project programme incorporated with other subcontractors in the same workspace.
This resulting offsite build process can be seen on a couple of our completed projects, Berol Yard in Tottenham Hale and at Williamson Heights in Wembley, where we shipped our large pre-built subassembly skids to site up to 80% complete.
Social Impact
London has a construction output of £35 billion a year and that output provides huge congestion and also contributes to poor air quality because we’ve got too much transport within the M25 and thousands of workers commuting in and out of the capital daily.
Even if the construction sites are elsewhere in the UK towns and cities, they’re on the road daily adding to the ever-increasing rush hour.
What I like with this shift in manufacturing as an economic enabler, is that if we take some of that construction activity outside of London, which in turn eases the pressure on London, which can only be a good thing, especially as I feel I live on the M4/A4 these days !”