How MMC Reduces Costs and Speeds Up Project Timelines
MMC solutions can provide a whole host of benefits aside from resulting in modern, fit for purpose, reliable structures. Costs can be reduced whilst also speeding the timeline of the project!
In this blog, we will share information regarding how MMC reduces costs and speeds up project timelines.
At Helec, we proudly offer multiple services to support building projects using renewable, sustainable, and low-carbon technologies. Our 17 years of experience provide us with the expertise to professionally handle the services of design and consultation, all the way to installation and performance monitoring.
MMC vs traditional builds, which is better?
Whether Modern Methods of Construction (MMC) are superior to traditional construction isn’t a simple yes or no answer; it depends heavily on the project’s specific needs and priorities. MMC offers compelling advantages, particularly regarding speed.
Projects employing MMC often see significantly faster completion times due to off-site manufacturing and the ability to conduct processes concurrently. The controlled factory environment inherent in MMC also allows for much tighter quality control, minimising the risk of on-site errors and defects.
Furthermore, the precision of factory production leads to reduced material waste, contributing to both cost savings and a more sustainable approach. Site safety is also generally improved with MMC due to the reduced on-site activity and the more controlled working conditions of a factory.
Finally, because a large portion of the work occurs indoors, MMC is far less susceptible to weather delays, leading to more predictable project timelines.
MMC limitations
However, MMC also has limitations. It can be less flexible when dealing with highly complex or bespoke designs that require significant on-site adjustments. The logistics of transporting large modules or components can present challenges and increased costs, especially for projects in remote locations or with difficult site access.
While MMC often offers long-term cost savings, it can require a higher initial investment in design and manufacturing setup. Moreover, MMC might not be the most appropriate choice for sites with limited access or challenging ground conditions that make module delivery and placement difficult.
Traditional construction
Traditional construction, in contrast, offers greater design flexibility, allowing for more complex architectural forms and easier on-site changes. It is also more adaptable to unexpected site conditions that might arise during construction. Traditional methods can also support local economies by utilising local labour and materials, a factor that can be important for some projects.
Traditional build limitations
Traditional construction typically involves longer construction times due to sequential on-site processes.
It also generally incurs higher labour costs due to the greater reliance on on-site workers. The less controlled nature of on-site work leads to increased waste compared to MMC, and construction schedules are often vulnerable to delays caused by adverse weather.
Ultimately, the optimal construction method depends on a careful evaluation of the project’s unique requirements. MMC is often advantageous for repetitive housing projects, schools, hospitals, projects with tight deadlines, and those where stringent quality control is paramount.
Traditional construction remains a viable and sometimes preferable choice for highly complex or bespoke designs, projects with challenging site conditions, and situations where supporting local economies through the use of local labour and materials is a key consideration.
How MMC reduces costs and speeds up project timelines
Modern Methods of Construction (MMC) offer significant advantages in terms of cost reduction and project timeline acceleration compared to traditional construction methods. Here’s a detailed explanation of how MMC achieves these benefits:
Cost Reduction:
- Reduced Labour Costs: A significant portion of construction costs is attributed to on-site labour. MMC involves manufacturing components in a factory setting, which requires fewer on-site workers. This leads to lower labour costs, reduced wage expenditure, and potential savings on associated costs such as insurance, training, and site management.
- Minimised Material Waste: Prefabrication in a controlled factory environment allows for more precise material calculations and cutting, significantly reducing the risk of over-ordering and minimising waste. This translates into direct cost savings on materials and disposal fees, contributing to a more sustainable approach.
- Improved Material Procurement: MMC techniques often involve the production of standardised building modules or components that can be replicated across multiple projects. This standardisation streamlines the procurement process, facilitates bulk purchasing of materials, and enhances economies of scale, leading to cost savings for developers and contractors.
- Reduced Preliminaries: On-site preliminaries, such as site setup, temporary works, and security, can be significantly reduced with MMC. As a large portion of the construction happens off-site, the time and resources spent on these preliminaries are minimised, leading to further cost savings.
- Predictable Costs: The controlled factory environment and standardised processes of MMC lead to more predictable costs. This reduces the risk of cost overruns due to unforeseen issues, weather delays, or material price fluctuations.
Speeding Up Project Timelines:
- Concurrent Processes: MMC enables concurrent processes, where different parts of the building can be manufactured off-site while site preparation and foundation works are carried out simultaneously. This significantly reduces the overall construction time compared to traditional methods where these processes are sequential.
- Faster On-Site Assembly: Once the modules or components are manufactured, they are transported to the site for quick assembly. This process is much faster than traditional on-site construction, where each element needs to be built from scratch.
- Reduced Weather Delays: As a significant portion of the construction takes place in a factory, MMC is less susceptible to weather delays, which can significantly impact traditional construction timelines.
- Improved Quality Control: The controlled factory environment allows for better quality control and reduces the risk of errors and rework on site. This leads to fewer delays and a faster overall project completion.
- Programme Certainty: The reduced reliance on on-site labour and weather-dependent processes leads to greater programme certainty, making it easier to predict and manage project timelines.
Further Considerations:
- Early Design Freeze: To maximise the benefits of MMC, it’s crucial to have an early design freeze. This allows for efficient manufacturing and reduces the risk of costly changes later in the project.
- Logistics and Transportation: Careful planning and coordination of logistics and transportation are essential to ensure the timely delivery of modules or components to the site.
- Upfront Investment: While MMC offers long-term cost savings, it may require a higher upfront investment in design and manufacturing.
By addressing these considerations and leveraging the advantages of MMC, construction projects can achieve significant cost reductions and faster completion times, leading to greater efficiency and value for clients and stakeholders.
Does MMC need specialists?
While regular builders can handle some simpler MMC aspects like foundations and finishing works, specialist expertise is crucial for successful MMC projects. Design, engineering, manufacturing, logistics, and complex on-site assembly often necessitate specialist companies.
Simpler panelized systems might be assembled by trained regular builders, but volumetric or complex systems require specialist installers. Collaboration between regular builders and MMC specialists is often the most effective approach, combining traditional skills with specialised MMC knowledge.
Increased training and upskilling within the construction industry are essential for wider MMC adoption.
Invest in MMC solutions
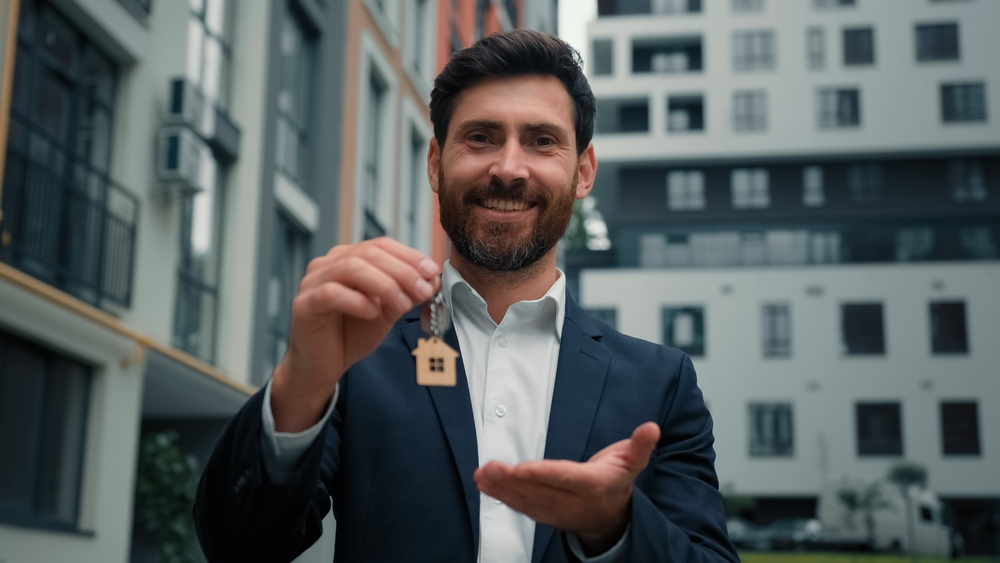
We hope to have provided everything you need to know by showing you how MMC reduces costs and speeds up project timelines. For more information on our financing options, feel free to click the link below for our contact information, so you can start your journey with us today.
The team here at Helec thanks you for taking the time to read our blog. If you have any further questions, you can contact us here. Alternatively, if you want to enquire about our expert services or for more information on our solutions, click here.
Our wide range of services enables us to provide consultation, installation, and maintenance if you require it.
Our expertise provides us the ability to offer the following energy solutions:
Combined heat and power packages
- Complete CHP service and maintenance packages
- Thermal stores and buffer vessels
- Ground source heat pumps
- Solar thermal systems
- Large district residential heating systems
And more. See how Helec can help you today.